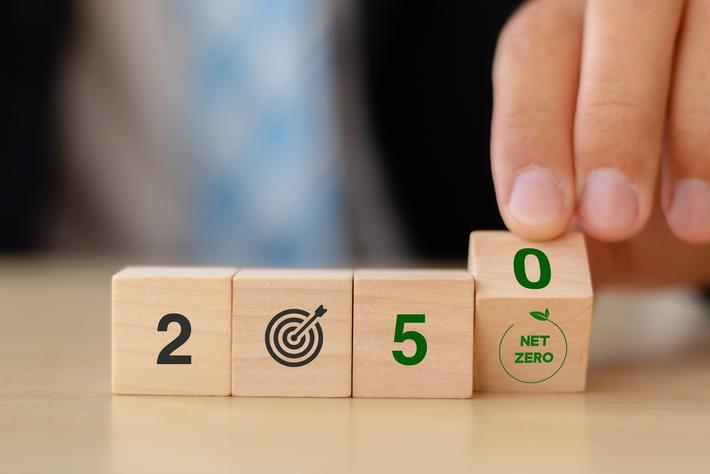
Pathways to decarbonization for the aluminum industry – 2050
A recent report from the International Aluminum Institute (IAI) outlines clear and comprehensive paths the aluminum sector can follow to reduce greenhouse gas emissions over the next 30 years.
The IAI position paper, Aluminum Sector Greenhouse Gas Pathways to 2050, presents a complete map of the path to reduce greenhouse gas emissions for the decarbonisation of the aluminum industry over the next three decades. The report is based on IAI's core knowledge and expertise of the global aluminum industry, including important data and analysis collected.
Aluminum is a determining factor for sustainable economic development. Being light, strong, durable, conductive and recyclable, aluminum products are essential elements for a low-carbon future. They provide energy-efficient and carbon-saving solutions to high-emission sectors that provide services, including energy, transportation, buildings, food and pharmaceuticals.
In 2018, the global demand for aluminum was 95 million tons, of which two thirds (64 million) were met by primary aluminum, produced from the ore, and one third (31 million) by recycled aluminum. Rapid demographic and economic growth over the next few decades means that global demand for aluminum will increase by up to 80% by 2050. This demand will be met by recycled and primary metal.
Despite the projected increase in the supply of recycled metal, IAI estimates that up to 90 million tons of primary aluminum per year will be needed in 2050. The organization said it is exploring realistic and credible technology pathways for sectoral reductions in greenhouse gas emissions by 2050 and for the decarbonization of the aluminum industry in line with the IAE and International Energy Agency scenarios.
Decabornization of the aluminum industry: scenario beyond 2 degrees
In a scenario beyond 2 degrees (Beyond 2 Degree - B2DS), the industry is expected to reduce its total emissions to 250 million C02e emissions, from a baseline of 1.1 billion CO2 emissions in 2018 and a Business asUsual scenario. expected by 2050 of 1.6 billion CO2 emissions. IAI has published a technical data sheet on the aluminum sector Beyond 2 Degree (2018-2050), outlining the scope, methodologies, data and analytical tools used by the IAI to calculate the current footprint of greenhouse gas emissions and model a 2050 scenario for the decarbonisation of the aluminum industry, based on the B2DS of the IEA.
Scope, emission sources and processes in the IAI datasets include:
- Full life cycle greenhouse gas emissions for semi-finished aluminum products;
- All processes from mining (primary route) and end-of-life collection (recycling route) to manufacturing, including ancillary materials, transportation, electricity generation and background processes;
- Global sector coverage (100%);
- Annual data, aluminum production from 2018 to 2050 and consequent process emissions. The sector's total GHG emissions currently amount to 1.1 billion tonnes of CO2 emissions.
IAI's input information for preparing the report included key data such as: historic primary aluminum production; data on recycling; historical emissions for all sources and processes; intensity of primary aluminum emissions, based on the IAI life cycle inventory (2015) and annual energy statistics, and aluminum production in 2050 and B2DS emissions.
The production data forecasts are based on the IAI 2020 reference scenario (March 2020). This dataset is updated annually.
The IEA has so far published two below 2 ° C warming scenarios: the Beyond 2 ° C scenario (B2DS) in 2017 and the sustainable development scenario (SDS) in 2020. For the IAT 2050 horizon, B2DS predicts an 85% reduction in total anthropogenic carbon dioxide from 34.3 billion CO2 in 2014 to 4.8 billion CO2, while the SDS foresees a 75% reduction on the 2019 baseline, from 35.7 to 9.4 billion CO2.
The sectoral budget 2050 of the IEA aligned to B2DS for the aluminum industry (250 million CO2 emissions) was calculated by adding:
- the direct CO2 emissions of aluminum published by the IEA under B2DS (171 million CO2 emissions);
- the assessment of the emissions deriving from the electricity consumption of the fusion (8 million CO2 emissions);
- estimated emissions from mining, counting electricity and greenhouse gases in non-smelting processes, transport and auxiliary materials (69 million CO2 emissions).
The IEA's B2DS budget for the aluminum sector includes a subset of direct industry emissions, with separate regional routes for the electricity consumed. The IAI then brought together the IEA scenario for direct CO2 emissions, generated by the aluminum sector and its energy consumption, and developed B2DS-aligned pathways for emissions not included in the IEA dataset.
The result is a B2DS-aligned path for the entire aluminum sector, which indicates the decarbonisation process and that by 2050 the total emissions of the aluminum sector covering the entire supply chain (production of bauxite, alumina and aluminum primary, recycling of pre- and post-consumer scrap and production processes of semi-finished products) should be reduced to 250 million (starting from the 2018 figure of 1,100 million CO2 emissions and from a Business asUsual (BAU) 2050 projection path of 1,600 million emissions) .
Of these 250 million tons, the emissions of electricity consumed in all processes, but in particular in fusion, would represent emissions close to zero. Currently, this source represents 700 million CO2 emissions, and in 2050 it would increase to 900 million, under BAU.
Non-electric primary aluminum emissions are expected to be reduced from 400 million today (over 520 million in 2050 under BAU) to less than 200 million.
Fuel combustion emissions from recycling and manufacturing processes are expected to be reduced by 55% compared to the BAU, from more than 110 to 50 million CO2 emissions.
Three paths for the decarbonization of the aluminum industry
To map the effective path for reducing emissions and decarbonising the aluminum industry, the IAI calculated all key data and identified three broad pathways, which would continue to meet the growing demand for metals: Path 1 - Decarbonisation of electricity; Path 2 - Reduction of direct emissions and Path 3 - Recycling and resource efficiency. All paths would involve a mix of technologies, including existing ones, some new solutions in development, and others yet to be developed.
Decarbonisation of electricity in the aluminum sector
The production of aluminum is an energy-intensive process, which requires significant amounts of electricity to break the strong oxygen-aluminum bonds of the raw material, alumina.
More than 60% of the 1.1 billion tons of CO2 emissions of the aluminum sector in 2018 come from the production of electricity consumed during the smelting process. By mid-century, in an IAE Beyond 2 Degree (B2DS) scenario, these emissions would be reduced to near zero, as fossil fuels would be phased out or replaced with carbon capture, use and storage (CCUS - Carbon dioxide Capture & Utilization or Storage).
Two-thirds of the sector's electricity needs are met by power plants owned and operated by aluminum producers. Most of these are fossil-based and are among the newest and most efficient in the industry. Decarbonised power generation and CCUS implementation offer the most significant emission reduction opportunity for these energy consumer-producers. Foundries, already connected to the grid, will have to reduce their electricity emissions by decarbonisingexisting grids. With the transition of the energy system to (intermittent) renewable energies, large and sizeable consumers of electricity, such as foundries, will play an essential role in stabilizing grids. In addition to the decarbonisation of the fusion process (already electrified), electrification and renewable energies could reduce the emissions of the main combustion processes in the sector (furnaces, alumina refineries and transport).
Reduction of direct emissions
The main sources of non-electricity emissions in the aluminum sector are the combustion of fuel, the consumption of smelter anodes, transport and the carbon footprint of raw materials. These sources are common to all manufacturers, with little variation in performance across the industry.
By 2050, under a slope alienated from IEA B2DS, the 650 million tons of Business AsUsual greenhouse gases emitted by these sources will have to be reduced to around 250 million tons, even as demand for the metal will increase by about 80%.
Direct emissions from the combustion of fuels to produce heat and steam make up 15% of the sector's emissions (2018) - from alumina refining, anode manufacturing, casting, remelting and recycling processes. For these thermal processes, electrification with low carbon sources offers a potential path towardsdecarbonisation. Where electrification is not feasible, green hydrogen, concentrated solar thermal energy and the use and storage of carbon dioxide (CCUS) are the best options.
Another 15% of the sector's emissions come directly from refining and smelting processes. Removing emissions from the smelting process is a common challenge for all manufacturers and will require profound technological change.
New cell technologies such as inert anodes, which emit oxygen instead of CO2, will play an important role in reducing emissions, although their use is currently very limited.
Auxiliary materials and transport emissions (which represent about 8% of the sector total) will be reduced through changes in other sectors and purchasing choices by aluminum producers. Unprecedented investments will be needed to deliver another 20 million tons of low-carbon primary aluminum, decarbonise the existing 65 million tons and build a 60-70 million tons post-consumer scrap recycling industry by 2050.
Recycling and resource efficiency for the decarbonisation of the aluminum industry
Infinite recyclability without loss of property is one of the unique advantages of aluminum. The recycling of post-consumer scrap today mitigates the need for almost 20 million tons of primary aluminum, avoiding about 300 million tons of CO2 emissions every year. When recycled metal is not held back in the economy, it is replaced by primary aluminum. Primary production today has a greenhouse gas emissions profile on average 25 times higher than the recovery of recycled metal. Aluminum recycling rates close to 100%, better scrap selection, elimination of pre-consumer waste and waste metal could reduce the need for primary aluminum by 20% by 2050. This would allow for a further 300 million tonne reduction in CO2 emissions in 2050, an impact of the same magnitude as the reduction in direct emissions under Path 2.
The path choices made by the protagonists of the aluminumindustry, says IAI, will depend on various factors, such as: unique energy supplies, availability of raw materials and scrap, regional policies, investment options and availability, speed and costs of development and implementation of the technology. Ultimately, sectoral and cross-sectoral partnerships will be needed to address this large-scale emission reduction challenge while meeting the growing demand for aluminum.
This transformation in the supply of aluminum requires action by everyone in the chain. It would also require policy frameworks that enable circularity and encourage investment in product design and innovations for efficient aluminum recycling.
Furthermore, with the cost of decarbonising the aluminum industry trillions of dollars, the key factor for the low-carbon industry by 2050 is choosing an investment to:
- supply up to 25 million tons of new smelting capacity and the decarbonisation of a capacity of 65 million;
- the 180 million tons of alumina capacity needed to meet the demand from foundries;
- the new carbon-free or CCUS technologies which currently constitute less than 1% of aluminum production, but by 2050 will have to satisfy more than 50%;
- the electrification of operations along the entire chain and the renewable grids that feed them.
Source: International Aluminum Journal