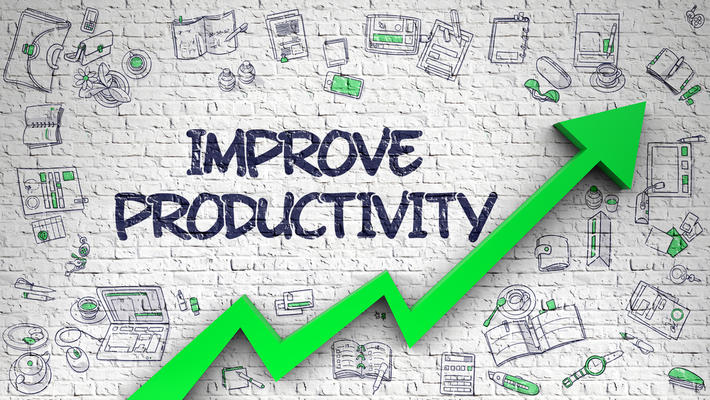
Increase the productivity and efficiency of die casting
With increased global competition driving the search for improvements in production efficiency, Ultraseal International Group talks about how innovations in release agents and spray technology can support the industry to improve productivity, efficiency and competitiveness.
In today's die casting industry, increasing productivity, optimizing costs and quality of output are key factors, especially in the face of increasing global competition and the need to produce increasingly complex components. These factors in particolar have encouraged foundries to search new solutions that enable the production of high quality, high quality cast components, reducing costs and improving production operations.
Developments in the automotive industry have led to a shift in die casting towards more complex and lightweight components in the powertrain, chassis and structural parts. The growth of the frame and especially the structure has led to investments in larger die casting machines and more expensive tools. This development has subsequently highlighted all aspects of die casting operations, including the role of the release agent used, as manufacturers seek to increase the productivity of the die casting industry, improving process reliability, output quality and increasing duration of the mold.
To understand how the choice of release agents can significantly contribute to the enhancement of production efficiency, cost reduction and business success, we need to take a look at the advantages that new technologies provide.
Maximize coverage effectively to increase the productivity of the die casting industry
If we think of the main purpose of release agents - to facilitate the release of clean parts and to avoid mold welding - obtaining uniform coverage is essential to increase production, to improve the reliability of the process and the overall quality of the final product. The use of traditional water-based lubricants leads to the evaporation of liquids when they come into contact with the hot steel molds, leaving a quantity of lubricated coating.
This is a critical step since an excess of lubricant does not allow liquids to evaporate fast enough when the metal is injected; however, an insufficient quantity of lubricant could lead to a poor flow of material or a poor welding of the mold, causing surface defects and porosity, compromising the overall quality of the piece. As the industry tries to meet the current demand for complex single-piece components, the complexity of the mold makes this problem more and more consistent, given the need to achieve a consistent level of lubricant coverage across the entire mold. Molds have cavities where excessive amounts of water-based lubricants typically remain, causing cold flows, porosity and stains on the casting surface.
The solution to this problem is found in electrostatic spray technology. Developed by Lubrolene, WFR-EC has an electrostatic charge added to the release agent which, when applied via a specially developed electrostatic spray gun, creates an enveloping effect and guarantees uniform coverage of release agents, regardless of the complexity of the mold.
The application of Lubrolene WFR-EC through an electrostatic spray further reduces welding problems and facilitates the removal from the water-based lubricant to ensure higher and more constant quality levels in die-cast components. The sum of the electrostatic charge with Lubrolene WFR-EC also greatly improves the adhesion properties and provides a more consistent oil membrane formation, which is essential for achieving uniform mold coverage and smooth release. In addition to the benefits in terms of quality, higher percentage levels of adhesion lead to a reduction in material waste and improved cycle times.
Usually, applying a water-based release agent with an air spray gun only achieves 4% of adhesion efficiency. The use of the spray gun technology specially developed by Lubrolene, on the other hand, improves the application of Lubrolene WFR-EC and achieves an adhesion efficiency greater than 80% compared to traditional water-based lubricants.
Process speed increase with spraying time to increase production
When trying to increase production and improve the efficiency of a process, it is often easy to overlook steps that have always been performed in a particular way. In die casting, the application of lubricating agents is one of these cases. As a short and repetitive cycle process, saving a few seconds in the diecasting process can lead to significant time savings and a direct impact on productivity and costs as long as the tool is designed accordingly.
If we observe the standard equipment for air spray application, to provide complete coverage and good adhesion of the mold, this type of tools must spray from multiple angles. The use of this equipment takes time and can compromise quality with uneven coverage levels, especially in more complex modules. Using electrostatic attraction, however, the Lubrolene gun can cover and adhere evenly to a much larger area, without the need to spray from various angles.
With a typical spray time - even for machines heavier than 4000 tons - of a few seconds, with specially designed Lubrolene WFR-EC spray heads and spray heads the spray time can be significantly reduced. This leads to a decrease in cycle times, an increase in yield and an increase in productivity. Additionally, the modularly designed Lubrolene spray equipment can easily fit any size die casting machine and its low maintenance design improves reliability, bringing potentially significant benefits to the die casting industry.
Increase uptime and reduce costs through increased tool strength
Quickly maximizing mold coverage can help manufacturers achieve greater levels of efficiency and increase productivity, but there is an added benefit to using Lubrolene WFR-EC that perhaps holds the most significant results: longer tool life. The use of traditional water-based release agents allows rapid cooling of the mold surface, leading to extreme temperature fluctuations that can quickly lead to the formation of cracks on the mold surface as a result of repeated compressive and tensile stresses. With cracks typically starting to form after a hundred shots, the tool life is reduced and the fewer shots available are around 120,000 in a typical die casting machine.
Thanks to its very small amount of spray, the rapid cooling effect prevalent in traditional methods is considerably reduced when using Lubrolene WFR-EC, almost eliminating the thermal stresses to which the dies would typically be subjected. By contributing to the extension of the tool's service life up to six times, the cost reduction can exceed € 500,000 per year. The longer life span of the equipment also implies fewer tools required, offering further savings on labor costs of up to 20%.
Overall, Lubrolene WFR-EC helps manufacturers increase production in the die casting industry, work more effectively, improve production efficiency, reduce costs and enable the production of more complex components that meet the needs of the industry. . A higher spray application speed means a significant reduction in cycle time; more uniform adhesion determines higher levels of process reliability and reduces material waste; and the reduction of the stress on the molds considerably increases their duration and resistance over time. The results of these fundamental advantages are evident, in fact they improve productivity and lead to a reduction in costs for the high pressure die casting industry, without compromising the quality of its production.