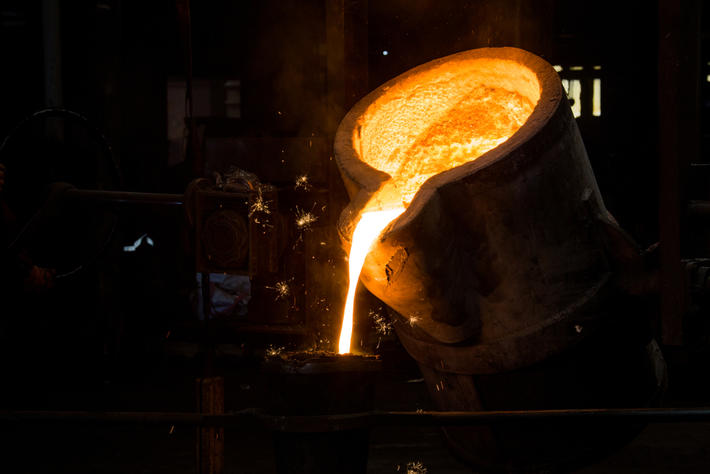
Foundry and smart manufacturing: key challenges for the foundry of the future
In recent years, the manufacturing world has been hit by the wave of new information technologies, whose main objective is to create integrated and connected factories, capable of generating large amounts of data. The elaboration and analysis of this real information treasure can bring enormous advantages in terms of efficiency and quality.
The foundry sector has proven to be very active and ready to welcome change: some important Italian companies in the automotive scene have become protagonists of important transformation projects. Overcoming these digitalization challenges is an essential factor in maintaining and improving one's competitive position, acquired with difficulty during decades of business development.
Industrial Internet of Things in the 4.0 foundry
One of the best known terms in smart manufacturing is Industrial Internet of Things: the application of tools from the consumer world, the Internet, for industrial purposes, such as the connection of sensorized machinery. Many plant manufacturers now provide these solutions already perfectly integrated, also allowing them to benefit from tax breaks.
But today's theme is Digital Transition, which is why we no longer speak of Industry 4.0 but of Transition 4.0. The transformation of assets is in fact only the first step, in which the production tools begin to generate a multitude of heterogeneous and unconnected data, but with great IT potential: one of the most complicated challenges is managing the resulting complexity, building processes and integrated flows to feed a single and transversal database. Thanks to this immense Data Lake, it is possible to manage the entire corporate production world from an overall view, making decisions based on organic data analysis and synthetic KPIs.
The collection of large amounts of data is also an enabling factor for Artificial Intelligence algorithms, which for some years have no longer been just a fascinating research topic but a concrete opportunity for the industrial ecosystem, especially through the branch of machine learning, the so-called Machine Learning.
Machine Learning for foundry quality and smart manufacturing
Many companies in the foundry and foundry industry interface with a highly competitive market, where customers require guarantees in respect and improvement of quality levels: raising this level a little requires a lot of effort.
An application of Machine Learning to overcome this challenge is PredectiveQuality Analytics: the link between process parameters and product quality is deepened in order to anticipate the onset of problems or, in the extreme case, waste.
Often when a qualitative problem is faced at a certain point in the process, there is a tendency to carry out a targeted local investigation of the problem: with the automated analysis it is instead possible to apply a global approach to search for the causes that could, for example, have led the onset of waste.
The tool is a predictive model that acts during a continuous process, such as a steel or cast iron casting, providing indications about the quality of the product during its production, monitoring the values provided by the sensors on the 4.0 foundry plants. The advantage is the anticipation of the qualitative feedback that is generally obtained only downstream of the process, in the testing and certification phase of the products before sale.
With connected systems you can do much more: customer feedback, or even the parameters collected through networked products, can provide great indications about the quality trend in the long term, significantly increasing the possibility of connecting product quality. with process parameters. It is not uncommon for some processes to be entrusted to subcontractors, from which further information can be collected to reconstruct the complete photograph of the life of the product before its marketing.
This is the world of connected supply chains: suppliers, subcontractors and customers become part of the production ecosystem in all respects, a single continuous stream of information collection. Through this trend, for example, production planning systems can be studied, to be able to find the meeting point between an excellent level of service and the optimization of production capacities and resources.
Automated processes of smart manufacturing
The result is an overall cohesive system, easier to manage and govern, where a data driven decision-making model is implemented, with effects not only on the production departments, but also on the administrative and financial departments of the 4.0 foundry.
RoboticProcess Automation systems are an example of this, able to support back-office activities by taking care of repetitive and mechanical data entry operations, such as the reconciliation of invoices with order and goods receipt and the automatic accounting of the document.
The value of integration into the 4.0 foundry
In an increasingly competitive market where in order to slightly raise one's quality standards it is necessary to produce great effort, the ability to apply advanced technologies to the multitude of data collected allows you to find new ways to achieve the goal, and place yourself in positions of advantage to customer's eyes.
It is crucial that companies seize the opportunities provided by digitalization, undertaking transformation actions with a global vision, relying on partners capable of "seeing" throughout the production process and helping the transition to smart manufacturing. Continuing to limit oneself to single specific interventions, on a single plant rather than on a single process, can generate a local benefit but certainly does not capture the disruptive change favored by global digital interconnection.
Source: In Fonderia – Il magazine dell’industria fusoria italiana, n. 2 – 2021