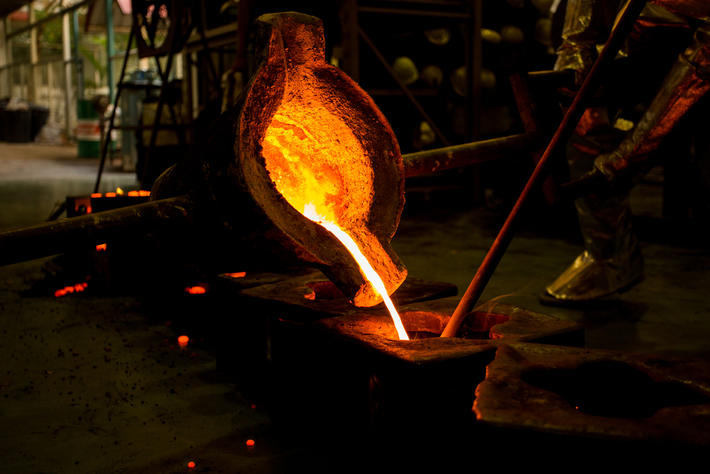
The decarbonisation of foundries: new objectives for maximum environmental sustainability
Despite the complicated economic situation of recent years, companies have continued to invest to reduce the environmental footprint of their products, obtaining important results.
More than twenty percent is the percentage of investments dedicated to the environment by companies in the sector out of the total gross investments in tangible assets: a truly significant datum, especially if compared to the ISTAT data relating to both industry considered as a whole (about 1. 5%), and to metallurgy understood in a broad sense, i.e. referring to the Ateco code 24, which falls within a range between 3.5 and 4%.
Numbers of this magnitude clearly show how it is now clear to companies in the sector that taking action to reduce the environmental impacts that foundry activities potentially entail is today, beyond the need to comply with environmental legislation, crucial in order to be able to guarantee important competitive advantage.
The growing sensitivity of civil society and public administrations towards these issues and decarbonisation is in fact leading to the development of environmental sustainability assessment and certification systems which, increasingly, involve not only the producers of goods or services intended for the consumer but also companies that produce intermediate components within subcontracting chains, as is the case with foundries.
Circular economy: the use of recycled materials as secondary raw material is increasing
The foundry is a central element of the "circular" economic model: in fact, the smelting activity has always represented the technique through which it is possible to use scrap in order to create new products. As such, the foundry company represents the essence of the concept of circularity which sees waste at the center of the activities aimed at its economic valorisation.
According to the data collected on a sample of companies representing 37% of the total production of castings in Italy, in recent years there has been a further slight increase in the use of recycled raw materials.
Non-ferrous metal foundries use only ingots of aluminum or other light alloys to charge the furnaces. However, this does not mean that the raw material used does not come from recycling: a large part of the ingots used by Italian non-ferrous foundries actually comes from the remelting, by refiners, of non-ferrous scrap from recycling. Furthermore, foundry products, whether they are made of ferrous or non-ferrous metals, have very long life cycles and, at the end of their use, can in turn be recycled to give rise to new products, in an eternal inexhaustible cycle.
Production waste: less volumes and more reuse for the decarbonisation of foundries
The foundry sector, especially the one with sand molding systems, is characterized by a high waste/net product ratio. The attention of companies in the sector, in recent years, has focused heavily on the methods of managing the residues of the various work processes, both for the purpose of reducing their quantities, encouraging reuse within the foundry processes themselves, and by researching possible alternative external reuses to the traditional disposal activity.
Emblematic of the trend towards the circular economy in waste management is the case of exhausted earth. In addition to the absolute decrease in the quantities produced, which went from approximately 575 kilograms per ton of castings produced in 2000 to 324 in 2019 (with a reduction of more than 43%), it is interesting to observe how currently more than 95% of the exhausted earth is recovered through external reuses in uses as raw materials in replacement of sands and earths from extraction, practically eliminating the need for disposal in landfills.
This trend is in full agreement, once again, with the principles of the circular economy, which intends to enhance production residues (waste or by-products) as "secondary raw materials" that can be used in industrial processes such as cement factories, furnaces, or still for the manufacture of construction and civil engineering products.
In order to further encourage this trend, the "Smelting slag" Technical Table was set up by the Lombardy Region. The objective of this initiative is to provide all those involved with a clear and shared technical-regulatory reference framework for the circular management of some of the main residues of iron and steel and metallurgical activities present in the region.
Climate-altering emissions: towards carbon neutrality
According to the study "Strategy for the decarbonisation of Hard to Abate sectors", drawn up by Interconnector Energy Italia and the Confindustria associations, in collaboration with the Boston Consulting Group, the seven most energy-intensive industrial sectors (steel, cement, paper, ceramics, chemicals, glass and foundries) produce a total of about 20% of direct greenhouse gas emissions in Italy.
Even if only a small part of these emissions is attributable to foundries, companies in the sector have long been committed to reducing their emissions of climate-changing gases and, in the coming years, they will be called upon to face a further and demanding journey, in technical and of economic commitments, towards the decarbonisation objectives set by Europe Precisely to outline a roadmap of the actions necessary to achieve carbon neutrality by 2050.
In fact, the Industrial DecarbonizationPact was signed, an alliance for the decarbonization of industry which aims to ensure a rapid and inclusive ecological transition, capable not only of achieving the objectives indicated by Brussels but also of preserving the competitiveness of international markets of sectors that represent the backbone of the Italian economy.
From a technical point of view, within the foundry sector, the main tool to refer to in order to achieve the required decarbonisation objectives is the electrification of companies. The second lever in order of potential impact concerns the use of biofuels in gas ovens.
According to the estimates of the study carried out by the Boston Consulting Group, by 2030 the complete electrification of cupola furnaces, the partial electrification (about 20%) of gas furnaces and the use of biofuels in the remaining 80% of gas furnaces would allow a reduction of direct CO2 emissions of approximately 50%. The complete electrification of the remaining gas-fired furnaces, by 2050, would lead to a 90% reduction in the direct emissions generated to date by companies in the sector.
The replacement of the current furnace fleet which operates using energy vectors such as coke and methane with electric furnaces will require not only a major economic effort, which will necessarily have to be supported by specific financial and/or fiscal instruments, but will also require interventions to make the amount of electricity needed; in this regard, the study estimates that in 2030 the electricity requirement of the hard-to-abbot sectors will be 64 TWh, of which approximately 40% is "green".
Furthermore, for the electrification process to be sustainable, important regulatory interventions will be necessary aimed at making the price of electricity competitive which currently, in our country, records a significant price gap compared to its European partners, also due to different management regimes of charges linked, for example, to indirect energy costs.
Dust emissions: drastically reduced thanks to new technologies
Another aspect on which companies in the sector have constantly worked in recent years is that relating to dust emissions: foundries, in particular those that use "disposable" sand forming processes, generate them in all phases of the production process , from casting to casting finishing. Even the permanent production of non-ferrous metal castings gives rise to particulate emissions, quantified in terms of "oil mists".
The use of BAT techniques (Best Available Techniques) and the development of end of pipe technologies have enabled the achievement of important objectives for the reduction of residual emissions. This trend was also recorded in the period 2017-2019 with an average -12.5% compared to 2015. The figure is even more significant if we consider that the level of emissions in 2015 was in turn -65% lower than in that of 2003.
Energy: more and more efficiency interventions
The issue of energy consumption for an "energy intensive" sector is not only a significant environmental aspect, in particular in relation to the issue of decarbonisation of foundries, but also one of the main cost factors for casting.
For all types of foundry, smelting activities absorb the prevailing share of energy: these account for 63% in cast iron foundries, 54% in steel foundries and 35% in aluminum foundries. It is therefore in this phase of the process that the most significant efficiency measures can be placed, as is evident from the analysis of the data contained in the "Guideline for the drafting of energy diagnoses in the foundry sector", created by Enea in collaboration with Assofond.
The Guideline helps to spread awareness of the importance of energy efficiency in the sector, provides companies with a concrete contribution and is part of the "Energy Efficiency Notebooks" series. It is an operational guide both for companies operating in the foundry sector and for professionals involved in the preparation of a "quality" energy diagnosis and compliant with Annex II of Legislative Decree 102/2014.
The publication contains the main energy consumption items of the production sites, the indications for the implementation of a monitoring system suitable for the sector, the energy performance indexes relating both to the entire plant and to some processes and, finally, a broad overview of the possible energy efficiency interventions present in the scientific and technical literature, together with an economic and energy evaluation of the interventions carried out and proposed reported in recent years in the energy diagnoses received by Enea.
It was precisely the analyzes carried out on the diagnoses that made it possible to quantify the energy savings identified and achieved by companies in the sector following the energy diagnoses carried out. These are important savings which, as regards the electricity consumption that can be saved, amount to a total of 86,800 MWh, corresponding to the annual consumption of 32,134 typical families. The 370 interventions actually carried out, on the other hand, have allowed companies in the sector to save a total of around 2,800 TOE (Tons of Oil Equivalent) per year.
Source: In Fonderia – ll magazine dell’industria fusoria italiana