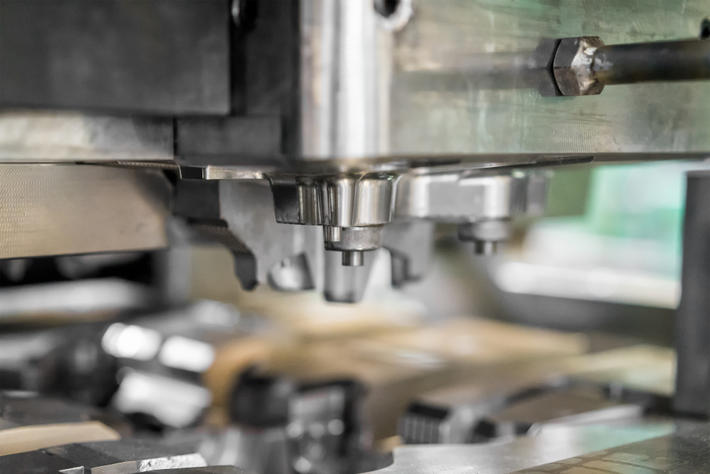
Choosing the best maintenance policy for die casting
Each company has its own critical issues, priorities and competitive dimension. This translates into different margins, customers with different needs and timing and therefore it is impossible to recommend a single strategy that is valid for everyone ...
In the die-casting sector, especially in molding, failure intervention is often preferred because it is believed to cost less than other maintenance strategies. This belief is based on the fact, for example, that the spare parts warehouse is kept at a low level.
However, at the time of failure, the downtime, in the event of a breakdown, is much longer than the short downtime that we would have had with organized (preventive) or even predictive maintenance: just think of any unavailability of personnel - for example for night stops - and technical times to find spare parts.
To continue to adequately serve the market, companies that choose the failure maintenance policy normally have higher safety stocks of finished or semi-finished products than those that rely on other maintenance policies. All this translates into longer stops, greater warehouses, greater immobilized product and therefore greater disadvantages and costs.
So how to get out of this uncertainty?
The answer is made up of three letters: TPM - Total Productive Maintenance
It is a mythology aimed at finding the best exploitation of plants, machinery and resources for aluminum die casting but not only. The goal is to minimize costs, increase production speed and, more generally, improve competitiveness on the market. Thanks to this logic, the choices of maintenance policies are reviewed, defining the best basic policy based on the characteristics of criticality and variability of faults.
More generally, the true essence of the TPM methodology is the delegation of maintenance operations to operating personnel. It is about overcoming the traditional division of tasks between maintenance and production workers, to create a shared competence capable of solving simple or medium-complexity problems in the aluminum die casting process.
In this way, a trained, cohesive and proactive work team is created that is sure to be successful for the company.
The differences are many, all to the advantage of the company that applies the TPM: downtime is reduced, the load on maintenance staff is lightened and the conscience of the machine operator is much higher, with undeniable benefits for everyone.
In summary: the productivity of the die-casting systems, the quality of the die-cast product and the operator's own knowledge of the machine lay the foundations for continuous improvement and an approach to improving maintenance.
Source: Costruire Stampi marzo 2020