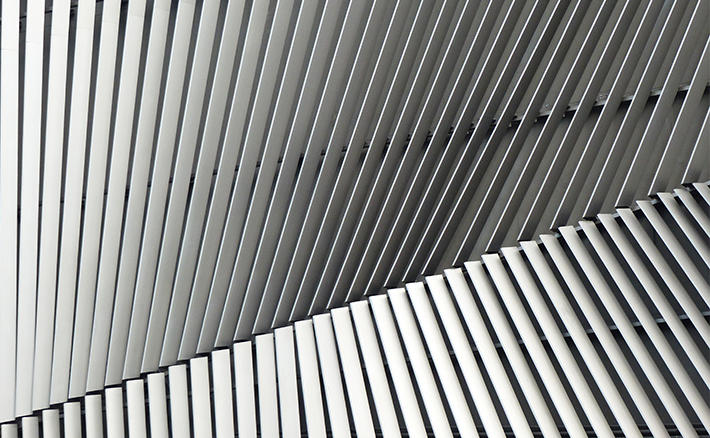
The mechanical properties of aluminum
The mechanical properties of aluminum are lower compared to other materials such as steel or titanium, but the low specific weight guarantees a saving on the weight of the component. The mechanical properties of aluminum, however, can be improved thanks to the possibility of melting the material with other elements such as copper, magnesium, silicon, manganese and zinc, through fusion processes. These products are commonly referred to "aluminum alloys" or "light alloys", because the specific weight is among the lowest of structural materials.
The mechanical properties to be identified to investigate the capabilities of a material such as aluminum are:
- Yield strength
- Breaking load
- Elastic properties
- Lengthening
- Compressive stress
- Fatigue
- Toughness.
The yield strength of aluminum
One of the most important mechanical properties is the yield strength, which indicates the point after which a material deforms under the action of the load. When a material is subjected to a load less than its yield strength, it deforms into measure proportional to the load itself but returns to its original shape when the load is removed.But if it is stressed further, the material is deformed in proportion to the load irreversibly.
Unlike steel, the loss of proportionality in aluminum alloys is not sharp and sudden. In aluminum the yield strength is conventionally defined as the stress that causes, in the stress / deformation curve, a deviation from the proportionality of 0.2% of the initial length. This load is also called "trial" and abbreviated as "Rp0.2". The yield strength for alloys with higher strength is about 85% of the breaking strength.
The tensile strength of aluminum
Among the mechanical properties of a material, the breaking load is identified as the maximum load it can undergo without breaking. It is not possible to find a unique data on the breaking load of aluminum because it depends on the alloy to which it refers: it is equal to one third compared to the steel.
The elastic properties of aluminum
In keeping with the comparison with steel, aluminum has a coefficient of elasticity equal to one third. In essence, its elastic deformation under a load is three times greater than steel. The low rigidity is often a structural advantage because in the event of impact stresses, aluminum can absorb energy in an elastic way, that is without incurring permanent damage.
The elongation of aluminum
The elongation consists in increasing the length when the material is subjected to traction. The elongation values for aluminum alloys can be from less than 3% of the initial length to over 35% for an annealed material. Treated alloys usually have an average elongation rate of about 8%.
Compressive stress
Among the mechanical properties of aluminum, measuring compressive strength is not obvious because it is a ductile material, besides the fact that pure deformation due to compression is a rarity. Consequently, by convention, the compressive strength of aluminum is considered equal to that of tension. However, the products derived from die-casting have a lower tensile strength than the compressive strength.
Fatigue
Fatigue means resistance to repeated vibrations or load cycles. Aluminum does not show a limit fatigue load, below which fatigue is not highlighted. To avoid problems, those who use aluminum in their projects must keep the loads below the fatigue limit indicated in the manuals.
Toughness
Toughness, among the mechanical properties, consists in the ability to resist breakage due to fragility. Aluminum alloys have less toughness than steel. Toughness in general depends on the thickness of the component: if it increases, the toughness decreases to a certain minimum value, which, once reached, remains constant.
To learn more about the mechanical properties of aluminum and the possibilities offered by die-casting, contact italpres.